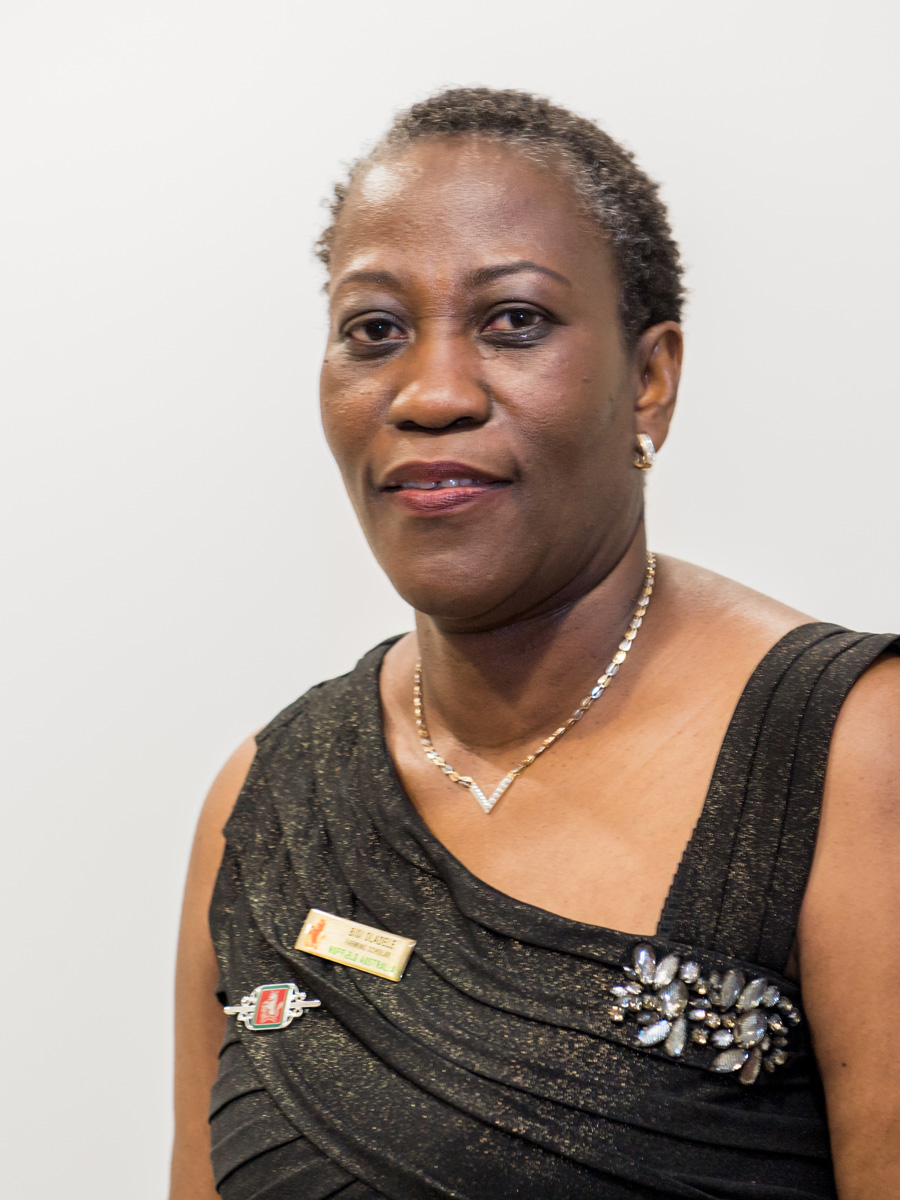
Olabisi Oladele
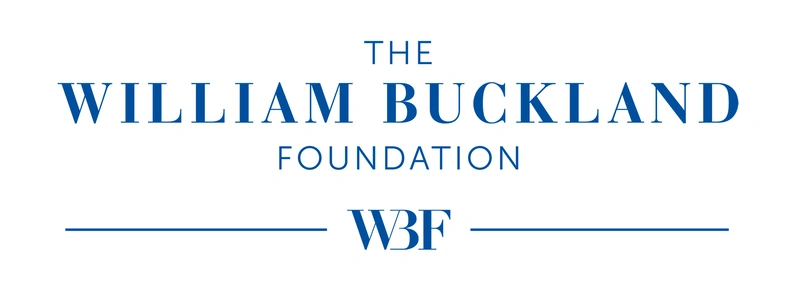
Nuffield Australia 2018 Scholar
Future gains in packhouse automation rely on workforce development
In the face of increasing automation in food production, it is critical we equip our current workforce with the skills they need to embrace this change and ensure the future viability of agriculture through awareness of career pathways for the younger generation.
That’s a key observation of 2018 Scholar, Dr Olabisi Oladele, who observed the ability of international educational programs such as that of the New Jersey Food, Agriculture & Natural Resources (FANR) Department to drive awareness of the benefits of a career in agriculture to potential industry entrants. Supported by The William Buckland Foundation, Dr Oladele travelled throughout Italy, France, the Netherlands, United Kingdom, United States and Canada, researching ways to promote career pathways in agriculture in the face of increasing automation.
“The adoption of automation in packhouses is imminent. To facilitate this new wave of automated operations, it’s important to understand the human capital requirements behind the change and focus on developing the future workforce. The New Jersey FANR is a division of the New Jersey Department of Agriculture. It runs programs to prepare young adults for leadership and careers in the science, business, education and technology of agriculture. This is done through the transformation of traditional agriculture or horticulture programs to STEM infused agricultural science programs, designed to give the agricultural workers of the future the skills they will need.”
Based in Orrvale, Victoria, Dr Oladele is Technical Manager at Geoffrey Thompson Holdings, a vertically integrated apple and pear horticultural business. Recognising the need to meet the increasing trend towards greater automation in packhouse facilities, Dr Oladele set out to better understand how the agriculture sector can facilitate adoption and change within the existing and future workforce. Her report outlines that while automation aims to improve productivity and reduce reliance on human involvement, the design of automated packhouse equipment means human capital is ultimately still required.
“Automated packhouses still need technicians to plan production, run the line and perform maintenance, preserving the need for human capital within these businesses. This presents an opportunity for businesses to both facilitate the uptake of automation and upskill their staff, to ensure they have the tools they need in a more automated workplace.”
The report includes a series of case studies on automated packhouses across Italy, the United States and Canada. The case studies reveal a range of different motivations and approaches to the implementation of automated packing processes.
“Near Merano, Italy, I visited the GEOS packhouse, part of the enormous Val Venosta Co-Operative. Founded in 1946, GEOS has a membership of 300 farmers and packs 70,000 tonnes of apples each year. GEOS has been using different automated processes for the past 24 years, include a pre-sizer, automatic labelling and a palletiser with an integrated weighing system. Despite this level of automation, the business has opted to use forklift drivers on the line, instead of replacing them with robots. Recognising the need for human capital during the three peak harvest weeks each year, GEOS opted to keep the drivers employed throughout the year, to support them and ensure they were available when needed.”
Dr Oladele’s report highlights that various factors influence a business’ decision making around the extent to which they adopt automation.
“Some businesses prioritise human capital and community support over immediate efficiencies, opting to train and upskill existing employees instead of replacing them altogether.
Ultimately, Dr Oladele concludes that with labour challenges continuing to be a key issue in horticulture and the wider agriculture industry, there is a need to better develop and prepare the next generation for careers in more automated industries.
“As an industry, it’s important to place a focus on strategic planning for the future. To build a strong collective workforce for the entire agriculture sector, we need to better develop the next generation through technology, educational initiatives, and new ways of thinking. In Australia, greater industry investment is required to raise awareness of career pathways and foster the development of potential employees in agriculture, to support both the growth of automated operations and the sustainability of the sector.”